A piece sculpted in clay, which is to become a limited series in bronze, must go through the molding process. A mold is simply a latex/rubber impression of the sculpted piece, reinforced with a plaster-like fiberglass shell. As shown, the shell is made in two halves bolted together. Over 50 good wax forms may be "pulled" from a good production mold; however, reputable sculptors destroy the mold when the limited series is completed.
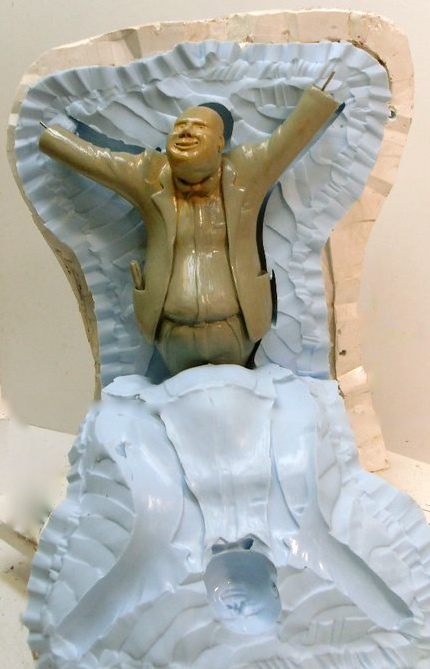
Soapbox Sam's primary mold is completed, and the original clay sculpture is being removed. Along with molds for each hand, molding wax will now be poured into this production mold so that the foundry process may begin.
A series of waxes of SoapBox Sam have been "pulled" from the production mold; these waxes have been cleaned up, or "chased", and now are ready to take into the foundry casting process. The Soap Box Sam series is limited to eight (08) completed bronzes; therefore, once "Sam the 8th" is finished, the production mold will be destroyed.
Most sculpted pieces in clay must be "dismembered" into a number of parts, so that it is possible to get a mold around, and then easily removed from, each individual part. The Three Sisters shown here had to be broken down into 19 separate molds. So, once the 19 individual parts are "pulled" from their respective molds, the wax parts must be reassembled by the artist, back into the original whole. The reassembled whole is then "chased" until the artist concludes the completed wax is ready for the foundry casting process.
Shown here is a casting bucket at the Artist's foundry. A slurry mixture is prepared in these buckets & waxes are then dipped into the slurry mix. Covered with slurry, each wax receives ultra-fine coats of sand for several days, building up a "ceramic" shell. When dried, the shells are heated to melt away the wax form inside (nick named "The Lost-Wax Method"). The ceramic shell, now hollow, is furnace hardened for the metal pouring process.
Once the ceramic casting shells are furnace hardened, molten bronze is poured into them. Daniel's Bull, 10.5"HX6"WX10"L, which required two shells, is shown being cast here. Once cooled, the casting shells are removed from the bronze sculpture parts.
Once the bronze is poured, the sculpture's parts must be braised & welded into the whole. Shown here, Leonardo (13"H, 9"W, 21"L) required five molds and shells. With all its legs now in place, the sculpture continues being "chased" (cleaned up), here on a leveling wheel.
After the pouring process, each raw bronze piece must be chased & polished to the point where the Artist determines the patina process (final finish) should begin.
Samantha & Hector shown here at the beginning of the patina process. Most finish work starts with the application of a darker bronze undercoat that is water washed & dried so that coloring & highlighting may begin.
Phil, with darker bronze undercoat applied & water washed, is shown here on the drying bench. Next, Phil will receive several layers of coloring chemicals which will be oxidized through patina flame working.
Phil shown receiving coloring chemicals being oxidized through patina flame working.
Leonardo shown receiving coloring chemicals being oxidized through patina flame working.
Hector & Samantha, shown here heated again by blowtorch, being brushed with some of the dozens of chemicals available for creating a rich variety of colors and patterns.
Anticipation, now beginning to cool, has its new patina coat. While the metal is still warm from the blowtorch, a generous coat of paste wax will be brushed on to protect the oxidized chemical coating.
Shown here is the Anticipation series (bronze on granite & steel: 7.5"H, 6.5"W, 10.75"L). Now on granite, with final patina detailing & wax buff out completed, the series will now be mounted on its steel stands & then packed for shipment. With this limited series completed, the mold is destroyed and, therefore, the bronze production process is completed.
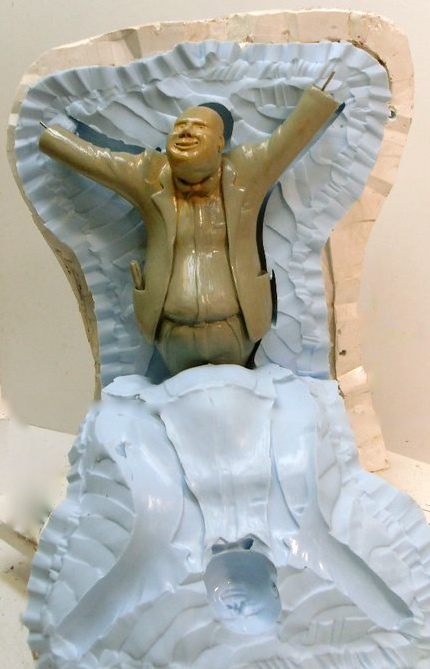
A piece sculpted in clay, which is to become a limited series in bronze, must go through the molding process. A mold is simply a latex/rubber impression of the sculpted piece, reinforced with a plaster-like fiberglass shell. As shown, the shell is made in two halves bolted together. Over 50 good wax forms may be "pulled" from a good production mold; however, reputable sculptors destroy the mold when the limited series is completed.
Soapbox Sam's primary mold is completed, and the original clay sculpture is being removed. Along with molds for each hand, molding wax will now be poured into this production mold so that the foundry process may begin.
A series of waxes of SoapBox Sam have been "pulled" from the production mold; these waxes have been cleaned up, or "chased", and now are ready to take into the foundry casting process. The Soap Box Sam series is limited to eight (08) completed bronzes; therefore, once "Sam the 8th" is finished, the production mold will be destroyed.
Most sculpted pieces in clay must be "dismembered" into a number of parts, so that it is possible to get a mold around, and then easily removed from, each individual part. The Three Sisters shown here had to be broken down into 19 separate molds. So, once the 19 individual parts are "pulled" from their respective molds, the wax parts must be reassembled by the artist, back into the original whole. The reassembled whole is then "chased" until the artist concludes the completed wax is ready for the foundry casting process.
Shown here is a casting bucket at the Artist's foundry. A slurry mixture is prepared in these buckets & waxes are then dipped into the slurry mix. Covered with slurry, each wax receives ultra-fine coats of sand for several days, building up a "ceramic" shell. When dried, the shells are heated to melt away the wax form inside (nick named "The Lost-Wax Method"). The ceramic shell, now hollow, is furnace hardened for the metal pouring process.
Once the ceramic casting shells are furnace hardened, molten bronze is poured into them. Daniel's Bull, 10.5"HX6"WX10"L, which required two shells, is shown being cast here. Once cooled, the casting shells are removed from the bronze sculpture parts.
Once the bronze is poured, the sculpture's parts must be braised & welded into the whole. Shown here, Leonardo (13"H, 9"W, 21"L) required five molds and shells. With all its legs now in place, the sculpture continues being "chased" (cleaned up), here on a leveling wheel.
After the pouring process, each raw bronze piece must be chased & polished to the point where the Artist determines the patina process (final finish) should begin.
Samantha & Hector shown here at the beginning of the patina process. Most finish work starts with the application of a darker bronze undercoat that is water washed & dried so that coloring & highlighting may begin.
Phil, with darker bronze undercoat applied & water washed, is shown here on the drying bench. Next, Phil will receive several layers of coloring chemicals which will be oxidized through patina flame working.
Phil shown receiving coloring chemicals being oxidized through patina flame working.
Leonardo shown receiving coloring chemicals being oxidized through patina flame working.
Hector & Samantha, shown here heated again by blowtorch, being brushed with some of the dozens of chemicals available for creating a rich variety of colors and patterns.
Anticipation, now beginning to cool, has its new patina coat. While the metal is still warm from the blowtorch, a generous coat of paste wax will be brushed on to protect the oxidized chemical coating.
Shown here is the Anticipation series (bronze on granite & steel: 7.5"H, 6.5"W, 10.75"L). Now on granite, with final patina detailing & wax buff out completed, the series will now be mounted on its steel stands & then packed for shipment. With this limited series completed, the mold is destroyed and, therefore, the bronze production process is completed.